工業4.0浪潮滾滾來襲,智能制造在世界范圍內如火如荼。盡管在機械加工方面,自動化技術已相對成熟,但受到程序復雜性、柔韌性、成本控制等多方面制約,裝配作業的自動化仍難覓令人滿意的解決方案。
在實際應用中,“標準化”設計的哈工大先步機器人表現出了傳統“非標”設計所沒有的優越性。
隨著國內首個標準化裝配平臺的落地應用,裝配自動化的困局有望得到緩解。這款裝配平臺名為“哈工大先步機器人”,由先步信息研發推出,上市不久便獲哈工大機器人集團數千萬級戰略投資。它的成功之處在于通過采用標準的模塊化設計,在較低成本的基礎上造就快速、精準、靈活的裝配表現,完成了對“中國智造”的生動詮釋。
裝配自動化,舊題未解又添新愁
與自動化機械加工生產線的加工對象是單個的機械零件不同,自動化裝配生產線主要從事產品制造后期的各種裝配、檢測等工序,其對象和程序的復雜性給自動化的實現帶來了挑戰。因此,雖然裝配在產品生產過程中非常關鍵,但傳統裝配技術卻相對落后,經常有部分人工操作的工序,用于代替技術上極難實現自動化或在成本上并不經濟的裝配工序。
據業內人士介紹,復雜產品的生產過程中大約1/3的人力在從事有關產品裝配活動,裝配工作占整個產品生產工作量的40%-60%,裝配費用占制造總費用的30%-40%,若在裝配中發生問題,將增加多達40%的制造費用,直接影響產品的整體生產周期。
此外,當今社會消費者對產品多樣化和頻繁更新迭代的需求與日俱增,更是給裝配自動化帶來了新的難題。加上人力成本上升等壓力,讓制造企業面臨著嚴峻的挑戰。
標準化設計,直擊行業痛點
“傳統的裝配技術已成為相關領域高效制造的巨大障礙”,哈工大先步機器人的主力研發者繆建偉表示,傳統的智能裝配線是個性化定制,設計上屬“非標”,雖能滿足用戶需求,但因設計周期長、可復制性差、投入不菲、運維成本高等問題,因此想要大規模推廣阻礙重重。出任先步信息首席科學家的繆建偉先后在瑞士、德國、新加坡從事智能制造科學研究,具有30年豐富的設計及項目、團隊管理工作經驗。
要從根本上解決“非標”設計的缺陷,核心在于“標準化”設計。這正是哈工大先步機器人的研發思路。據繆建偉介紹,哈工大先步機器人由凸輪驅動抓取機器人、輸送模塊、機架模塊、電控箱、平臺軟件5大部分組成,抽象出不針對裝配對象的標準化設計,軟硬件、結構標準化率超過70%,只剩下30%的針對裝配對象的“非標”工作。
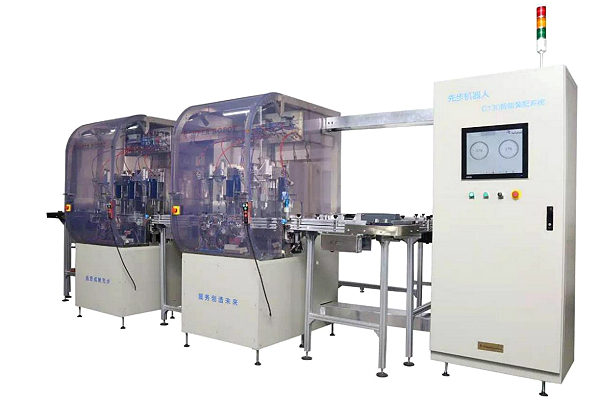
在實際應用中,“標準化”設計的哈工大先步機器人表現出了傳統“非標”設計所沒有的優越性。
首先是在裝配速度上。一般一臺單臂多軸機器人相當于一只手,只能同時執行一個動作,而哈工大先步機器人是個“千手觀音”,可以根據需要裝配的零件數和工程的復雜性裝無窮多的“手”。繆建偉表示,一個需要7-10個人才能完成的溫控器零件裝配,哈工大先步機器人可以憑一己之力獨立完成。
其次是精確度。“哈工大先步機器人是標準化、模式化運作的,所以設定完成后,它點到點之間的裝配誤差就很小,也就是說它不僅高效,能節省大量人工成本,而且精確度很高,誤差不會超過半根頭發絲大小,可以說基本無誤差。” 繆建偉說。
此外,哈工大先步機器人的優勢還體現在企業最關心的投入效益上??娊▊ソ榻B,傳統六軸機器人造價貴,而哈工大先步機器人利用的則是原始的凸輪技術,造價低,安裝、調試、維護也簡單,這就大大降低了企業智能化改造的成本。同時,歸功于其模塊化設計賦予的高度柔性,企業能輕松改裝與擴充,以應對瞬息萬變的市場情況。
技術賦能,獲得先發優勢
傳統裝配技術之所以難有突破,在于其改進難點重重。而這樣一臺在速度、精確度、效益上都可圈可點的裝配平臺得以問世,依賴于研發團隊過硬的實力。據繆建偉介紹,哈工大先步機器人的研究成功得力于先步信息 16年航天軍工的技術沉淀。作為國家高新技術企業、重點軟件企業的先步信息,擁有國務院政府特殊津貼專家、國家 863 計劃專家團隊。
繆建偉表示,這臺機器人的技術在全球范圍內都是領先,并且是全國首個國內標準化裝配平臺,它的原創靈感則來自于古老的紡織機。 “凸輪技術在幾千年就有了,這個機器人是利用最古老的原理,加入了最先進的技術,來為工業機械生產提供最經濟的自動化解決方案,尤其是對于小型化的作坊和工廠,更高效和現實。” 繆建偉說。
據悉,這臺先步機器人目前正在申請專利合計130件,其中發明50件、實用新型70件、外觀2件。目前已授權40件。
自身的技術優勢為哈工大先步機器人的品牌口碑提供了有力支撐,幫助其在裝配自動化市場上獲得了顯著優勢。目前,這個機器人在手機電子行業的應用已初見成效,以后將運用于醫療、新能源等領域。“我們將通過行業解決方案的調整適配不斷拓展新的應用領域。” 繆建偉介紹。